There are five types of “computer numeric control” (CNC), each with pros and cons. A successful CNC project begins with identifying the right equipment for the job. To better understand the different types of CNC machines and their capabilities, you must first be familiar with the function of the axis.
Understanding CNC Machines and the Axis
CNC works by subtractive methods. That is, pieces of raw material are removed until a desired shape or pattern has been achieved. One of the most important pieces of equipment on a CNC machine is the axis because this is what determines the full range of motion for the machine and all of its tools.
A multi-axis machine (more than 3 axes) is almost always used to complete larger projects because it is able to move across all directional planes with greater ease. The more axes a machine has, the larger it will be, and the more skills a programmer will need to keep track of all of the separate movements.
3-Axis CNC Machines
Known for versatility, speed, and the ability to automatically change tools in the middle of a job, a CNC machine with a 3-axis design is the workhorse of many CNC studios. One axis moves the tools vertically, one moves them horizontally, and one moves the tools to different depths.
This is called the “XYZ” setup:
- X-axis is the vertical plane.
- Y-axis is the horizontal plane.
- Z-axis is depth.
- Decorative panels
- Finished parts
- Internal framing
- Jig cutting
4-Axis CNC Machines
4-axis CNC equipment also has the XYZ setup, but there is additional power along the X-axis for more advanced cutting along the vertical plane. A 4-axis CNC machine can cut holes and make incisions through both sides of material that a 3-axis machine simply cannot power through.
4-axis CNC services are especially good for:
- Intermittent cutting
- Unremitting (nonstop) cutting
- Engraving
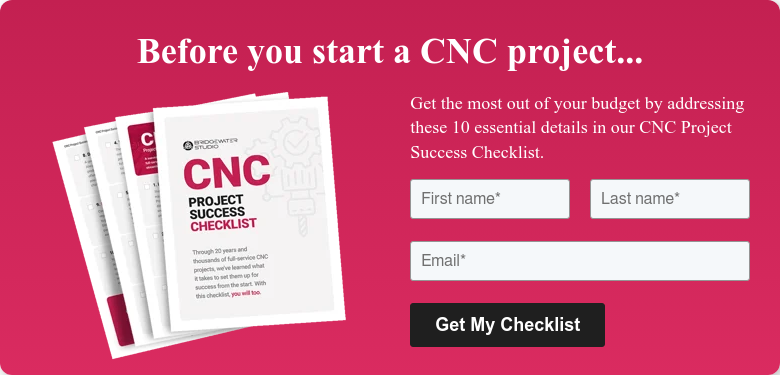
5-Axis CNC Machines
A CNC machine with a 5-axis design includes the original XYZ setup and introduces the B-axis, which rotates around the Y-axis for even greater cutting precision along the horizontal plane. This means the machine can perform a 180-degree rotation around the XYZ axes for extreme precision and accuracy.
5-axis CNC services are commonly used in boating, aerospace and automobile projects where extreme precision cannot be sacrificed in any way, shape or form. Some CNC machines are not truly 5-axis, but rather a different design called “3+2”, and these machines are limited to more rigid cuts.
6- and 7-Axis CNC Machines
Any CNC machine above 5 axes can produce highly complex 3D shapes and designs. These machines are perfect for any project where numerous materials have to be constructed together – for example, any instance where wood components need to be made with matching holes for steel reinforcements.
A fabrication studio with 6-axis or 7-axis services will be comparatively expensive because of the necessary expertise. Ask for examples of their 7-axis CNC services to make sure the studio knows how to use the equipment properly. Cross-referencing their work with other experts is a good idea.
From small engravings to large-scale sculpture and architectural elements, several factors will determine the right type of CNC equipment to use.
Types of CNC Machines
1. CNC Lathes
CNC lathes are the most compact CNC machines in existence and have the least amount of parts. They can only be fed materials in a single linear motion and are generally good for creating small components such as screws, bolts, shafts, and other types of metal fabrication, but not for creating large interactive environments and art installations.
2. CNC Routers
CNC routers hold a piece of material in place while rotating cutting tools move all around at a high rate of speed. The high rotational speed is the driving force behind the cut and the result is fascinating 2D and 3D designs.
CNC routers are used to cut softer materials like wood, plastic, acrylic, foam, and soft metals; however, its high-performance speed means even the lowest setting is still too fast to cut denser materials like aluminum or steel, which will quickly wear out machine components.
The main functions of a CNC router are:
- 3D cutting
- 3D carving
- Engraving
CNC routers efficiently carve precise shapes from a variety of materials.
3. CNC Milling
CNC milling machines are similar to CNC routers except they rely on torque instead of rotational speed, operating at speeds slow enough to cut through tougher materials like aluminum and steel without damaging internal components.
CNC mills move along the X and Y axes but do not have the ability to move along the Z-axis to control depth, making them best for projects that need thick material cuts.
4. CNC Laser Cutting
CNC laser machines produce exact cuts and are the best for engraving materials with the highest accuracy. The laser works by heating the material until it melts into a new shape and is best used on sheet materials. CNC laser machining can be used for the entire project or finishing touches.
5. CNC Plasma Cutting
CNC plasma cutting machines use a form of electronic ionization to heat the air to 50 thousand degrees Fahrenheit to create a plasma torch that can melt through almost anything, making clean cuts in even the hardest of materials.
However, since the process requires extreme electricity, the material must be electrically conductive:
- (Stainless) steel
- Aluminum
- Brass
- Copper
Bridgewater Studio Knows CNC
Even though different CNC equipment uses different tools, all of them are directed by a computer program that controls their every action. Without a custom program to tell them exactly how to move, they will not move at all.
Bridgewater Studio is a full-service strategy, design, production, and digital fabrication studio that can program highly complex CNC tasks with up to 7-axis equipment for maximum project accuracy and results.
Our six-step process ensures all project stakeholders are able to see and agree on a digital rendering before production begins. Once complete, the final product looks 100% like the original design. We take all of the guesswork and frustration out of bringing complex design concepts to life. Learn more about our comprehensive approach to digital fabrication and experiential project design by booking a no-obligation strategy session with Bridgewater today.