Plastics may be the most ubiquitous material on earth — used for everything from baby bottles to aerospace parts, and everything in between. The invention of plastics and plastic fabrication technologies transformed manufacturing and the world. Lightweight, flexible and capable of being molded and shaped in ways other materials could not, plastics enabled inventors and brands to achieve new levels of innovation.
Plastics also allow creators and designers, brands and businesses to express their unique personalities with custom furnishings, graphics, fixtures and artworks.
In this article, discover what plastic fabrication is and how plastic fabricators transform plastic into a universe of useful, amazing and innovative items. We’ll also discuss how new technologies help plastic fabrication companies minimize waste when building with plastic.
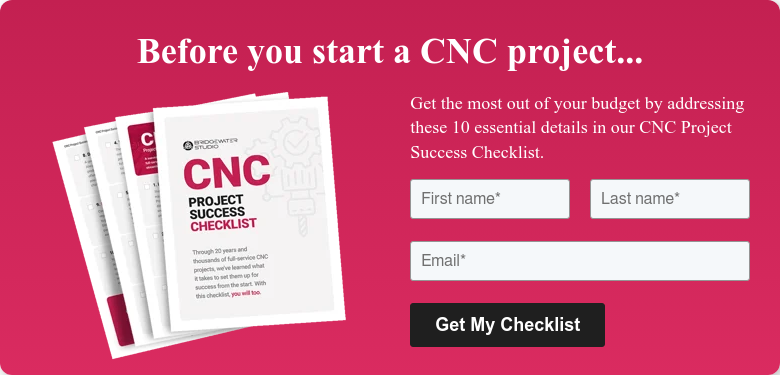
What is plastic fabrication?
Plastic fabrication refers to the process of making objects out of plastic or its precursors such as synthetic resins and other synthetic or semi-synthetic polymers. The process of plastic fabrication involves multiple steps beginning with planning and design and concluding with the manufacture, assembly and finishing of the planned object.
The first plastics and methods of plastic fabricating were popularized in the late 1800s with the development of Celluloid, and then, Bakelite. While today, we view plastics in the context of their lasting impact on the environment. Early plastics were a valued substitute for materials made using natural resins harvested from plants and insects which were sometimes difficult to obtain.
Since these early beginnings, of course, the types of plastics used for manufacturing and the methods of fabrication have proliferated. Modern plastic fabricators employ tools and methods, such as resin printing, to minimize waste while continuing to use processed plastic when it is the best choice for the desired outcome.
What types of items are made using plastic fabrication?
A quick look around most built spaces will reveal many examples of objects made from plastic. We use plastics to build containers, furniture, household tools and appliances, and medical equipment and devices. Plastics are often used to encase or insulate other materials such as electronics. Shoes, jewelry and sports equipment are built from plastics as well.
Beyond the products we use day-to-day, specialty plastic fabricators are the secret ingredient behind some of the amazing objects used in special effects, experiential environments, exhibitions, public art, sculptures and location-based entertainment venues.
What methods and tools do modern plastic fabrication companies use to design and manufacture 3D objects using plastic?
Today’s designers and manufacturers have a wide range of tools and technologies from which to choose when making objects or parts using plastics. Many of these methods leverage plastics’ thermoset capabilities to create objects that hold their form permanently once transformed. Other methods employ thermoplastics which can be heated to form and then reheated to use again.
Some of these methods, such as stereolithographic (SLA) 3D printing, fabricate pieces using plastic precursors. In the case of SLA 3D printing, liquid resins are used. This base material is converted to plastic as part of the printing process.
Plastic manufacturing methods include both additive and subtractive processes. For example, a filament 3D printer uses an additive process–plastic is introduced to build a shape. Subtractive devices such as CNC machines, carve, mill or use other methods to remove material from a solid piece to fabricate the desired object.
Leading plastics fabrication methods include:
- CNC machining. Computer numerical control (CNC) refers to a method used to send instructions from a computer assisted manufacture (CAM) file to a machine. The device can then manufacture the designed object precisely and accurately. Different types of CNC machines use distinct methods to carve or otherwise craft objects from a substrate, including plastics. Common methods include grinding, hot wire cutting, milling or drilling.
- 3D printing. 3D printers use additive processes to construct objects using either plastic filament that is heated and shaped through an extrusion process or plastic resins that are formed into an object through a curing process.
- Laser cutting plastic fabrication uses a laser beam to cut a solid piece of plastic into the desired shape. Polycarbonates and acrylics are often shaped using this technology.
- Hand and/or extrusion welding employs heat to bind two pieces of plastic together. This method only works when both pieces are made with compatible plastics.
- Edge finishing, forming, and polishing processes smooth and shape the edges of an object. For example, a cutting board may be first molded or cut from a piece of plastic before given a smooth edge finish to make it safe for handling and more attractive.
- Drape /oven forming fabrication methods employ heat to soften a sheet of plastic and form it around a mold. Sometimes, a second mold is placed on top of the sheet to fully shape the piece in a process also known as pressure forming.
- Vacuum forming. This method of plastic fabrication also involves a mold. Once the heated plastic is placed over the mold, suction is used to pull it into place. The completed object is removed after the plastic cools.
- Injection molding involves injecting liquid plastic resin into a mold. A single mold can be created to create multiple pieces which facilitates mass production.
Custom fabrication or cut to size plastic. Specialty plastic fabricators can make custom pieces by building a negative mold to cast the item using liquid resin. Similarly, using CNC machines, laser cutting or other tools, fabrication specialists can craft one-of-a-kind objects from plastic sheets or blocks and by combining plastic components with other materials.
This wall installation at LinkedIn headquarters in Chicago was made using a custom mold and liquid resin.
What types of plastics are used for fabrication
Of course, different types of plastic materials yield different results. Some plastics become hard and rigid when cured. Other plastics retain their flexibility. Objects can be crafted to have a soft, rebounding layer or elastic characters that allow it to stretch and return to its original shape.
These capabilities to change form or return to form make plastics the first choice for many applications, from consumer goods to industrial machine parts.
10 types of plastics commonly used for plastic fabrication
- Acrylic, a transparent thermoplastic also known as polymethyl methacrylate (PMMA) or the branded product, Plexiglas.
- Polycarbonate plastics which are also transparent and impact resistant.
- ABS or acrylonitrile butadiene styrene which is the plastic used to build Lego bricks. Fused deposition modeling (FDM) 3D printers use ABS filament to create objects using computer assisted manufacturing (CAM).
- Ultra High Molecular Weight Polyethylene (UHMW or UHMWPE) is a thermoplastic characterized by its high impact strength. Its resistance to corrosion and wear makes it suitable for use in industrial settings.
- Polyethylene Terephthalate (PET or PETE) is another thermoplastic polymer and is used to create polyester. Some filament 3D printers use PET-based filaments.
- High-Density Polyethylene (HDPE) plastics are used in a wide range of products and are characterized by their high melting point and impact resistance.
- Polyvinyl Chloride (PVC or Vinyl). More than just the material that you stick to when you sit down in a chair during the summer, vinyl can be fabricated to retain its shape or flex.
- Low-Density Polyethylene (LDPE) has what is called low-temperature flexibility. This material will flex in cold temperatures instead of cracking. This material is not a good choice if structural strength is a priority.
- Polypropylene (PP). This widely used plastic appears in everything from cosmetics bottles to machine parts. Because it is resistant to chemical corrosion, PP is often used for cleaning supply bottles. The material also shows up in medical tools and car interiors.
- Polystyrenes. In extruded or expanded varieties, polystyrenes are lightweight and water resistant. Artists, exhibition designers and fabricators, and special effects teams use expanded polystyrene (EPS) to craft 3D objects using subtractive methods including CNC milling or carving.
Choosing the best materials for your project begins with choosing the right fabrication partner
Plastic fabrication is just one way that brands and businesses can build objects for their interiors, exhibitions, and activations. Is it the best choice for your next project? Let a team of experts help you decide.
Building customized pieces using plastic fabrication is just one of the many services a full-service planning, design and fabrication company can offer your business. Schedule a no-pressure introduction to Bridgewater Studio today to find out what other design and production tricks we have up our sleeve that can help you realize your next great project or concept. We’ll discuss your goals and the strategies, methods and materials to help you achieve them on time and within your budget, plus you’ll receive a free customized project plan, so you’ll be set up for success from the start.